RING-SHAPED DIES
Dies for pellet mills
Ring-shaped dies are the most common type of die, used for high-density products. This die delivers high productivity and allows high compression ratios. It’s used for compound feeds, as well as for a wide variety of other products: alfalfa, sugar beet, fertiliser, minerals, wood, straw, household and industrial waste, and more.
Manufactured from forged rings, Ferotec’s ring-shaped dies provide guaranteed strength and can be adapted to all types of product.
At its historic facility, Ferotec provides technical expertise throughout the production process, including heat treatment. Our know-how allows us to cater for all types of requests from our partners, including all types of die with cylindrical, conical, or clamp fittings.
Each die is unique and specially adapted to the most demanding productivity and durability criteria. Our sales advisors are on hand to provide service – right alongside the users of Ferotec dies. Depending on the product to be pelleted and user expectations, the type of bore, the alloy, the percentage of open surface area, and the counterboring type can all be adjusted.
A number of different factors
are involved
in improving a die
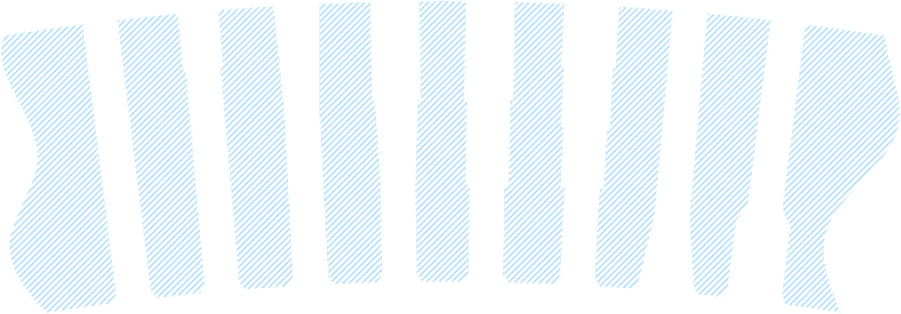
Different types of drilling
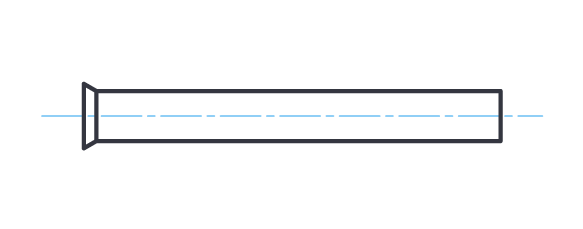
Standard drilling
Feed other
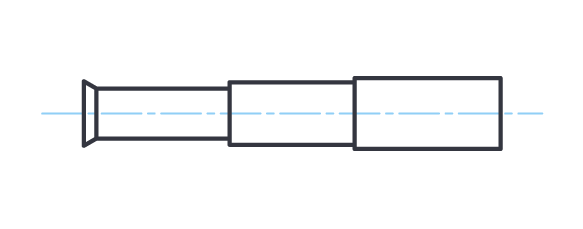
Double counterboring (cylindrical):
Biomass
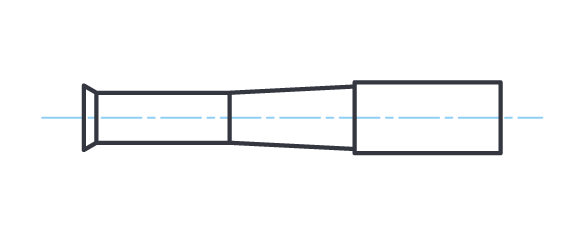
Double counterboring: conical/cylindrical
Biomass Alfalfa and sugar beet Minerals Other
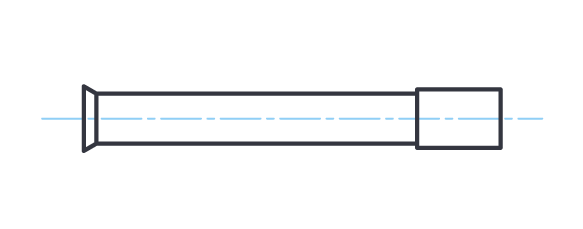
Cylindrical counterboring
Feed Biomass Other
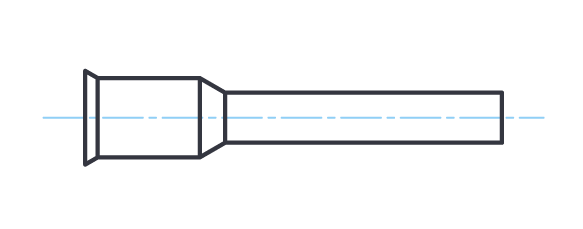
Cylindrical inlet
Feed Alfalfa
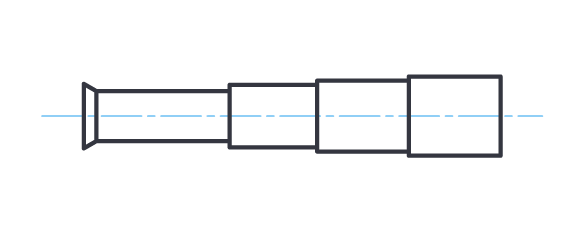
Triple counterboring (cylindrical):
Biomass
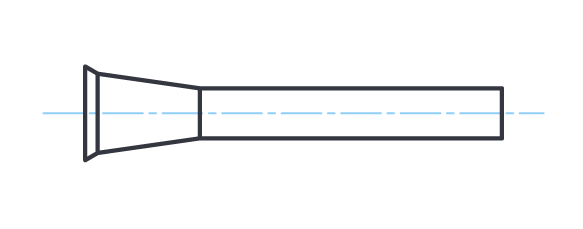
Conical inlet
Feed Alfalfa
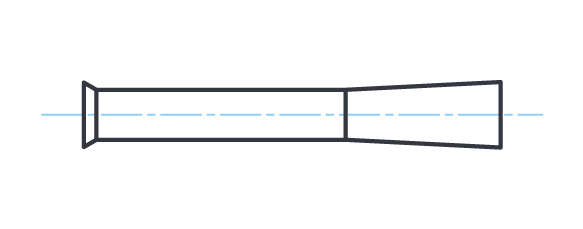
Conical counterboring
Feed Biomass Minerals
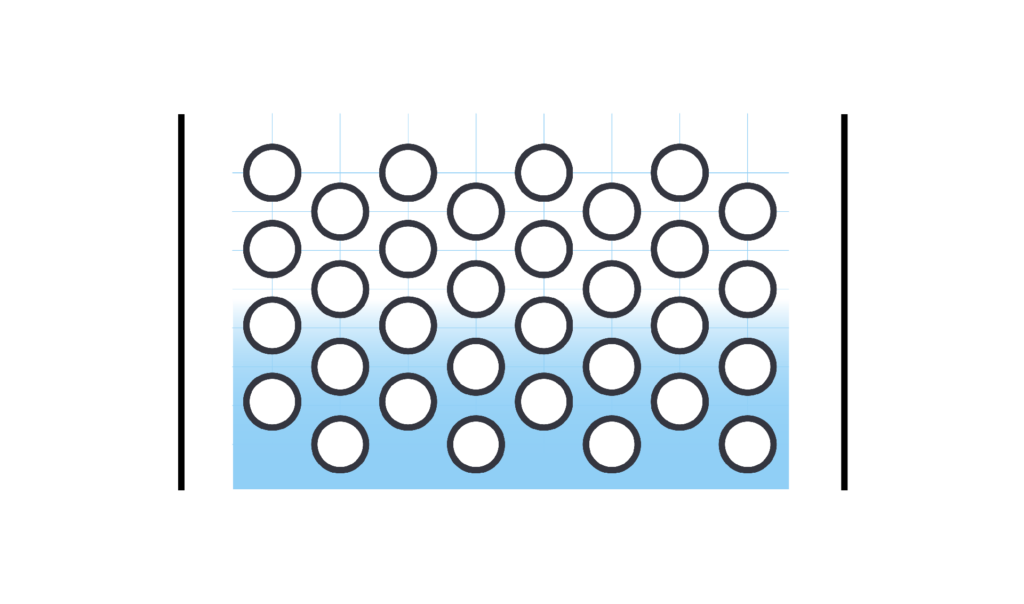
Diagonal drilling
Standard hole pattern
This hole pattern is known as “standard” and is the most widely-used. It ensures a strong die, with uniform distribution of the stresses it undergoes.
Benefits
Diagonal drilling is suitable for all types of product (including feed, biomass, and minerals) and shell type (dimpled or corrugated).
Limits
This layout does not optimize productivity, because the product takes more time to enter the holes. There are also no power savings. Energy consumption is not reduced.
Parallel drilling
Optimized hole pattern
Benefits
With more rows and fewer holes per row, this layout is suitable for higher flow rates. The product passes through the die quickly, with less wear on the track: this cuts the risk of the holes becoming clogged. Die peening is more uniform. Fast product throughput results in power variations decreasing by 3-10%.
Limits
For best results, this type of drilling requires proper adjustment of the gap between the rollers and the die, and the use of a dimpled shell without chamfer. The most visible benefits are for poultry feed.
The die is less stress-resistant, because there is less metal between the rows.
Note: parallel drilling does not provide more holes than standard drilling. Only the hole pattern differs.
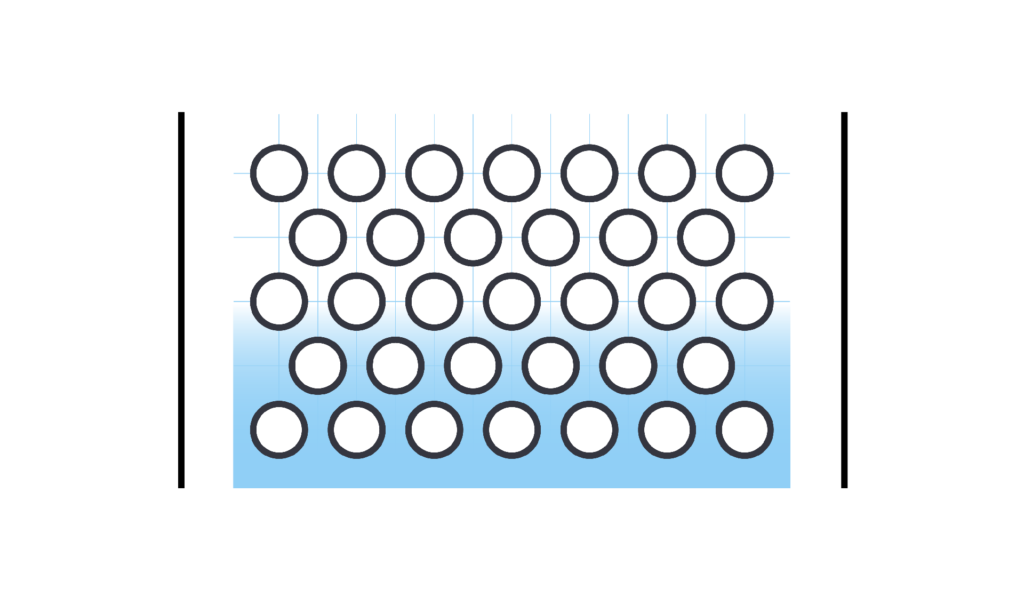